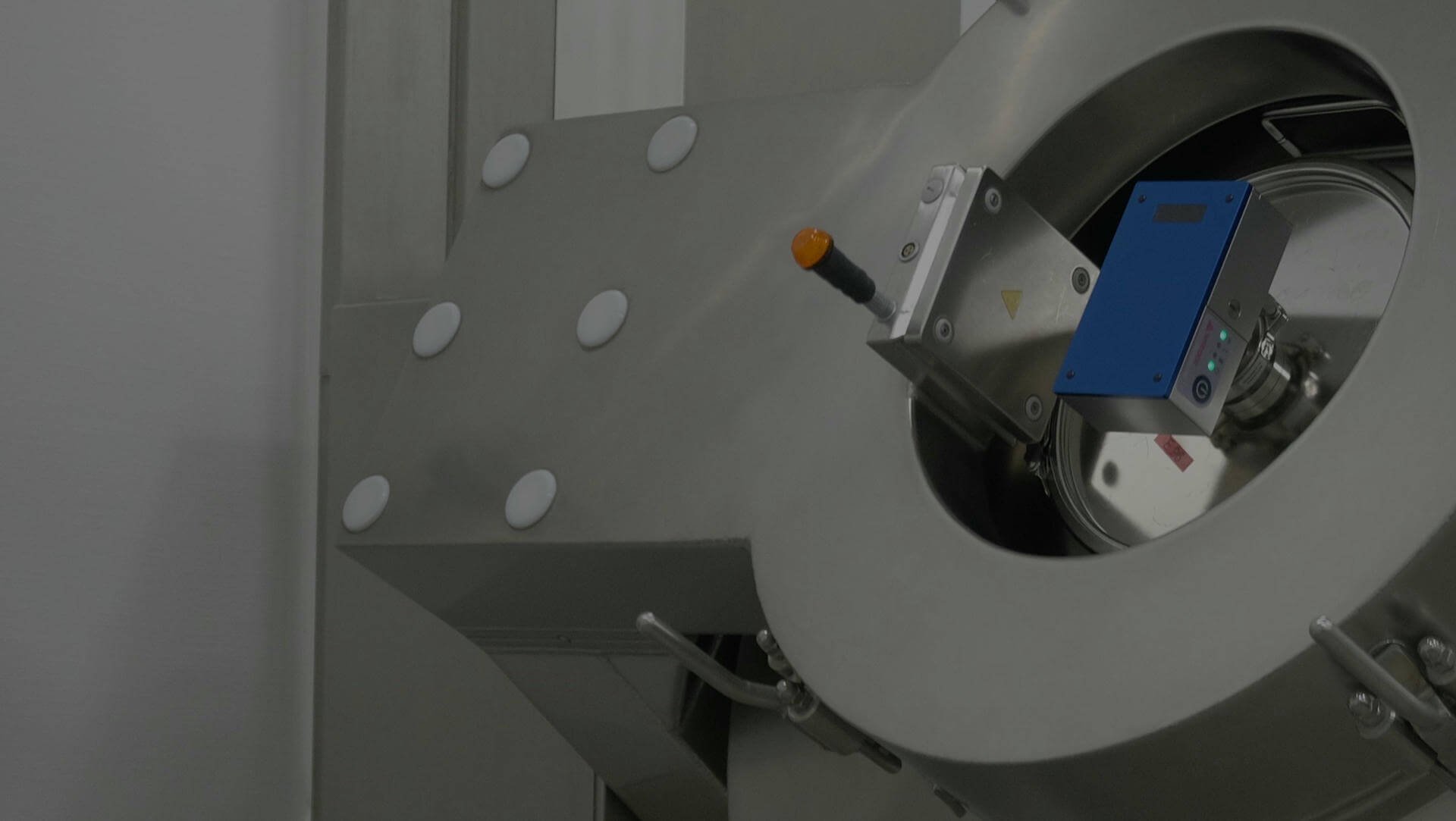
Optimize Pharmaceutical Powder Blending with NIR PAT
NIR-based Process Analytical Technology (PAT) enables real-time monitoring of blend uniformity, ensuring precise identification of the endpoint in pharmaceutical powder bin blending. This approach eliminates the need for traditional sampling and lab analysis, reducing delays and variability. By preventing overmixing, NIR PAT solutions enhance product quality, optimize production efficiency, and reduce the risk of wasted resources.
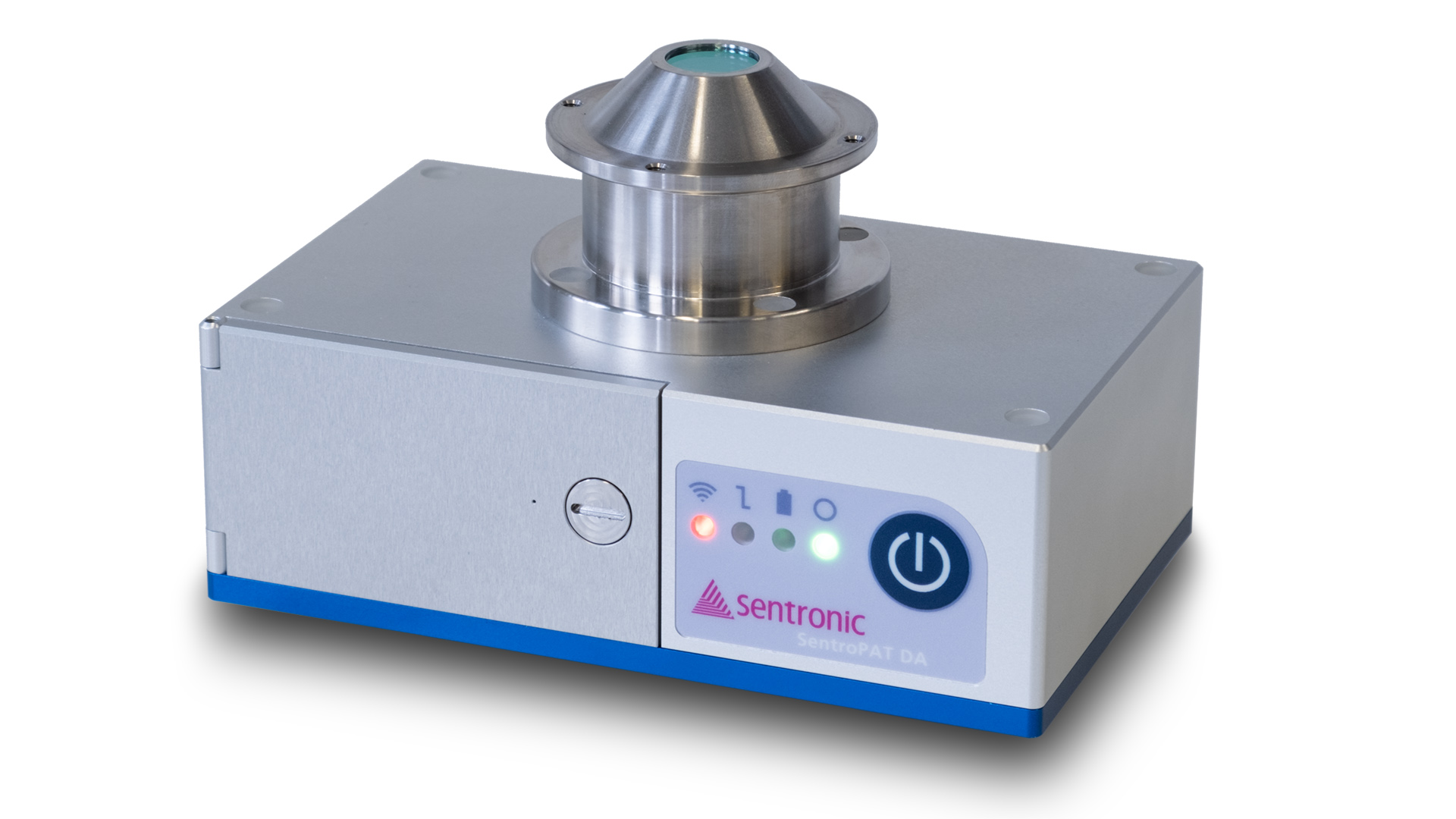
Blending is often a critical process in the manufacturing of solid oral dose pharmaceuticals. Product homogeneity and further processing steps can be adversely affected by improper blending. Traditionally, blending has been monitored by collecting samples from the process using a sample thief, which are then analyzed off-line in a laboratory. Unfortunately, this analysis does not provide information in real-time during the blending process. It also does not provide information about the blending process that could be used for process optimization.
By measuring near-infrared (NIR) spectra on-line using process analytical technology (PAT), such as a SentroPAT BU, the blending endpoint can be determined easily during the blending process. NIR Spectra can be collected during the blending process, often at a frequency of one, averaged spectra per blender revolution. The resulting NIR spectra can be easily processed to provide a qualitative analysis of blend homogeneity or quantitatively predict API content using more advance chemometric models. Such analyses can provide information that easily enables blending time optimization, which helps prevent faulty batches and over-blending.
The use of PAT can justify not performing conventional thief sampling and laboratory analysis of blends, both of which slow down the manufacturing processes and raise production costs. This makes PAT a valuable tool in process and formulation development, scale-up, and routine operation. Additionally, thief sampling can induce blend segregation, so technology that avoid its necessity may be advantageous for product quality. Once it is fully implemented, the PAT-enabled online monitoring of blend uniformity can be a critical part of a real-time release strategy.
PAT measurements are routinely used for the real-time prediction of many blending process characteristics, such as the blending end-point, blend uniformity, and active ingredient content. It is possible to determine which of a given product and implement only those. SentroSuite GMP software has implemented the most commonly used methods to calculate process characteristics, such as:
- Simple spectral statistical calculations, such as Moving Block Standard Deviation and Moving Block F-Tests, to determine the blending end-point. These techniques can be applied on raw spectra or can implement spectral preprocessing methods.
- Peak Area or Peak Height of NIR absorbance bands can be used to predict API content in a blend.
- Principal Component Analysis (PCA), which can be implemented using a SIMCA or Unscrambler X model, can be used to qualitatively assess whether a blend looks “normal” or may require further investigation.
- Chemometric methods, such as Partial-Least Squares (PLS) are also available through SIMCA or Unscrambler X, can be used to quantitively predict the API or
functional ingredients content of a blend.
Mounting options
Several mounting options are available to enable the use of the system with different scale and types of blenders. Contact us, if you need help with you specific integration requirements!